 |
等 级:长老 |
经 验 值:655 |
魅 力 值:194 |
龙 币:2304 |
积 分:1050.2 |
注册日期:2004-10-19 |
|
|
|
称霸全球汽车市场,丰田要过四道关(二)
——关口一:单纯依赖日本员工已到极限
迅猛扩张导致的人材不足;悄然而至的品牌老化;全世界对丰田一枝独秀的嫉妒;凡事依赖以往成功经验。这四道由于企业强大而产生的关口,丰田该如何渡过?不超越今天的丰田,就没有丰田的明天。
最近一段时间,表面平静的丰田内部正忙得四脚朝天。生产、开发、采购部门的工作人员频繁地在日美两国之间穿梭。原因是丰田的制胜法宝--产品质量发现了隐患。
最为严重的就是给丰田带来一半多利润的北美地区。最近几年投诉件数开始增加,甚至出现了要在过去根本不可能出现的问题。去年,“Sienna”微型面包车因为油箱故障而停止供货2周就是其中一例。而美国调查公司JD Power and Associates公布的2004年初质量调查结果对丰田而言更是雪上加霜。
今春发表的这项调查,是以购车时间在90天以内的每百辆新车用户的投诉问题作为指标实施的。按厂商来分,尽管丰田依旧排名投诉最少的第1位,但在得分上与其他竞争对手的差距却迅速缩小。在按品牌分类的调查中,尽管高级车“雷克萨斯”(凌志)仍排名第一,但“丰田”品牌却被“本田”和韩国“现代”等厂商超越,仅排名第8位。至于去年针对年轻人推出的新品牌“SCION”,更是出现了排名倒数第4的坏结果。
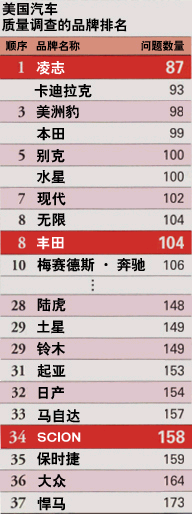
雷克萨斯主要由日本及加拿大的工厂制造提供市场的,因此如果单看美国工厂的话,情况就会严重得多。在北美地区实施的汽车制造厂质量调查中曾于2000年排名第一的丰田肯塔基工厂,由于其主力车型“佳美”在改型过程中产生的混乱,从2002年开始该厂排名迅速下滑,2004年跌到了第14位。
质量是丰田在北美地区打造高级品牌的生命线。这条生命线上开始亮黄灯,对丰田而言自然不能视若无睹。而且,如果对问题追根溯源的话,最终会归结到丰田总部的组织结构及企业文化。
原因是多方面的。一是丰田心目中的质量与消费者要求的质量产生了差距。JD Power and Associates公司亚太区总裁莲见 南海男指出,“尽管丰田在耐用性及车辆故障等性能方面水平很高,但在乘坐舒适性及造型设计等感受性方面,仍有很大的改善空间”。
在车辆功能不断提高,消费者意识不断变化的过程中,用户所要求的质量内涵也在不断改变。比如,按照以前空调是否制冷的质量标准制造汽车的话,那么现在空调的有效制冷所需时间,送风口噪音等就会成为用户不满的对象。JD Power公司的调查也在根据消费者的上述变化,逐渐增加对感性和汽车吸引力的提问。丰田正是在这方面没有能够全面跟上形势。
在美国出现的故障中就有这样的案例。美国用户经常使用的定速巡航系统开关,为了让用户不需把手从方向盘上拿开就能操作,安装到了方向盘的后面。然而,消费者反而不满,表示“位置看不见,不好用”。
还有车钥匙上附带的行李箱开关按钮也是如此。在行驶过程中如果不注意按了一下,行李箱便打开的话会很危险,因此就采用了持续按2秒钟才能打开的方式。然而这样一来,消费者却纷纷反映说“行李箱打不开”。
问题在于尽管这些意见的绝大部分都已反映到经销商那里,但却没有充分地传达给公司总部。其原因就在于过分自信和想当然。丰田每当增加新功能时都会在上市之前,通过消费者调查确认该功能会得到用户支持才会导入。此时丰田方面就会产生作为汽车专家的自负,以及已经得到消费者认可的想法。然而,实际购车的用户的想法与被调者的想法会产生微妙的差异。而丰田此时却不能灵活应对。
另外,在美国丰田还存在组织结构上的问题。由于生产、销售和开发等各项职能均由不同的公司负责,因此缺乏横向交流。结果,即便出现了问题,大多也都是由各部门与日本方面单方面协商。
当然,丰田对此也并没有袖手旁观。一年半前丰田制定了一个名为“EDER(EarlyDetection,EarlyResolution。早发现、早解决)”的对策,从总公司技术部及质保部等部门向美国丰田汽车销售公司选派了大约25名工作人员,旨在及早获取和解决客户意见。因为“与技术部门或者工厂能够直接对话的必须是相应的专家,而且和日本方面有沟通渠道的人”(负责美洲业务的专务董事稻叶良睨)。
此外,丰田还把在美国访问经销商服务店、收集消费者信息的调查员人数增加到了1000人,大概为过去的10倍左右。另外,还成立了多个由美国工作人员参加的项目。美国丰田汽车销售公司社长布野 幸利表示,“今后并非事事都要和日本方面联系,而是将在北美范围内主要针对美国车型迅速地解决用户问题”。
使质量问题迟迟得不到解决的另一个主要因素是人材不足。中国、南美和中东欧等地区的项目一个接着一个,人材供应跟不上。
肯塔基工厂的一位日本高层就曾毫不隐瞒地表示,“目前约有40名员工出长差,到刚刚开工的墨西哥工厂。我们也想踏踏实实地改善产品质量,但心有余而力不足”。
为了改善人手不足的局面,该厂正在积极实施改进措施。引进日本工厂普遍采用的SPS(Set Parts System,成套配件系统)就是其中的一例。这项措施就是在把配件向生产线上搬运时,按照便于装配的顺序排列,取消了生产线旁边的配件架。这样,生产线上的工作人员就不需再从架子上选择配件,哪怕临时工等熟练程度不高的人也能立刻适应。
然而,对于此类改善措施,必须要有推进的管理人员。作为年产能力50万辆的肯塔基工厂来讲,这就需要有大量的人员才行。这就出现了为了解决人材不足问题而需要更多人材的矛盾。
这种苦恼还涉及到对配件厂商的指导工作。“质量传教士”——在日本丰田有一个被人这样称呼的队伍,他们为了改善产品质量而奔走于各配件厂。木下 光男专务董事说,“虽然美国也有一些类似的工作人员,但规模较小。在汽车配件中按成本来说大约有7成是采购的,在配件厂方面出现问题的比例也基本上相同。本来我们希望在这方面进一步强化的”。
上述问题折射出来便是单靠日本人的局限性。丰田生产调查部资深人士、日本埼玉县科技大学(Institute of Technologists)教授田中 正知强调指出,“虽说业务遍及全球,但丰田终归还是日本公司。生产方式属于个人的思维范畴,没有能够将它清楚地向欧美人解释的理论”。
丰田对这个问题的一个解决方案是去年7月在元町工厂的厂区内设立的“全球生产推进中心(GPC)”。该中心接收来自海外生产基地的一线管理人员,在按照喷漆和组装等工序而设计的模拟生产线上进行实际培训。可同时满足130人的培训要求,目前已经完成了日本国内外大约2000人员工的培训任务。“2008年以前预计还要再培训3000人”(常务董事伊奈功一)。
GPC的目的在于生产的全球标准化。模拟生产线上的培训内容与实际生产线上的作业情况完全相同。不同的是培训人员会不时地看一下旁边的电脑屏幕。屏幕上的“视听手册(VM,visual manual)”正以影像形式显示操作示范。VM目前已经包括2000种工序。
在GPC,指导人员都来自丰田日本国内的工厂、且工作年限在25年以上的熟练职工。负责生产管理的内山 田竹志专务董事介绍说,“每一项标准作业都凝结了员工的智慧,选用的都是最高效的方法。作为改善生产的措施,大家过去各自都形成了自己的风格,而今后将在全球运用统一的最佳方案”。
丰田还准备在欧美、泰国和中国等地区设置GPC分支机构。到那个时候,日本的GPC就将起到为各分支机构培育指导人员的作用。因为目前来这里的辅导人员由于来自不同的工厂,所传授的内容不一样,导致海外工厂出现生产一线标准混乱的现象时有发生。
尝试全球同步更新车款
丰田目前正准备利用GPC进行一次规模宏大的尝试。这就是“全球同步更新车款”。现在,丰田的每一家工厂在新车量产前都要在生产线装上实物,对质量和各工序的效率等进行检测。这种作业由于必须要有来自日本的支援,因此过去的做法是首先在日本国内最先实施,经过一段时间后再横向运用到海外工厂。
丰田正在将试产过程统一到GPC中,以便在全球同步开始新车的生产。如果能够省掉海外工厂的最后检测工作,那么“在新车开始量产之前就不再需要日本方面的支援。从整体来看,也将能够将支援工作量减少一半”(伊奈常务董事)。
然而,GPC采用的模式化人材培育方式也有矛盾之处。丰田强大的根源就在于生产一线的员工通过自行寻找问题,一边反复摸索、一边解决问题,而且这种模式总是处于不停地进步之中。虽说只是基础技能,不过,GPC采用的一开始就提示最佳操作方法的培训方式,与过去的企业文化具有相背离的部分。
白水 宏典副社长就透露说,“大野 耐一先生(丰田生产方式的创始人)过去只是会问‘要是你,会怎么做?’,而不会说出答案,因此员工只能通过独自思考来掌握操作技能。公司里尽管也有人不认可GPC的做法,不过为了应对海外业务的急剧扩大,除了GPC以外别无他法”。
丰田在北美地区出现质量隐患还有一个原因就是对丰田生产方式缺乏指导。曾长驻美国丰田的现大发工业副社长箕浦 辉幸表示,“尽管美国的工厂一直都在强调连问5个‘为什么’的重要性,但几乎没有提供这样的训练机会。所以,即使模仿了丰田模式,到了具体的场合下还是不会思考问题”。
“互捧俱乐部”——,在肯塔基工厂里干部之间有时会说出这样的话来。丰田模式的信条是越是坏消息,越要尽快公开,以便让大家查明原因。但是与日本人相比,美国人如果受不到表扬,就很难维持工作动力。再加上语言障碍,因此日本管理人员即使发现了问题,大多也不会在众人面前把问题挑明。
最有代表性的是,花时间进行指导、不断培育人材的丰田生产方式虽然是丰田的优势,但也有可能成为其全球化的障碍。
“丰田2006年问题”。最近这种说法已经悄悄地业界传开。这一年既是德克萨斯工厂的开工时间,也是佳美进行全面改型的准备时间。除此之外,全球各地的工厂也将进行车型改进。是人材最为紧缺的一年,丰田很可能在此面临巨大考验。
另一方面,通过将感性知识转变为理性知识高效培育人材的GPC尝试,到时也应当在一定程度上确立下来。名冠全球的丰田生产方式到底是不是一种能够经受得住全球化考验的生产方式呢?答案恐怕要等到两年后方能揭晓。(未完待续)
|
|
|
|